NOAH MAUCK

Screwdriver Project
Lessons Learned
In this project, I learned the importance of safety and paying attention. The processes in this project felt the most intimidating to me. In order for these processes to be safe, paying attention to the teacher's instructions was paramount. Taking good notes helped me feel confident that I was taking the right steps in the manufacturing process and doing them safely.​
​
My advice for future students is to always ask questions if you are unsure of anything. The teachers and GTAs were always happy to help. Your safety is the first priority, and that is only possible if you are comfortable with the machines. You will produce a higher quality product if you feel comfortable and confident.
Cost Estimation
The cost breakdown for the flathead screwdriver is shown below:
-
Tool Rod (O1 Steel) - $1.09
-
Cast Aluminum Blank - $7.02
-
Labor - $384
-
$24/hr average machinist pay​
-
16 hours of labor spent machining, sanding, and finishing
-
This results in a total estimated cost of $392.11.
​
If I were to make 10,000 of these screwdrivers by hand, this would take around 6,500 days and cost $3,921,100. Obviously, this is not cost effective or time efficient.
​
If we assume a largely automated system and no labor costs, these 10,000 screwdrivers would cost $141,100 and take 417 days to produce. Each clock would be then worth around $14.11. This is under the assumption that the automated machinery costs 6$/hr and can produce one screwdriver per hour.
​
The cost breakdown for the Phillips head screwdriver is shown below:
-
Phillips Head Shank - $0.89
-
High Density Polyethylene - $0.10
-
Labor - $12
-
$24/hr average machinist pay​
-
30 minutes of labor spent injection molding
-
This results in a total estimated cost of $12.99.
​
If I were to make 10,000 screwdrivers by hand, this would take around 208 days and cost $129,900. This is more reasonable, however, than the other manufacturing processes.
​
If we assume a largely automated system and no labor costs, these 10,000 screwdrivers would cost $14,900 and take 34 days to produce. Each screwdriver would be then worth around $1.49. This is under the assumption that a robot costs 6$/hr and can produce one screwdriver every 5 minutes. Here we see the benefits of injection molding in mass production.
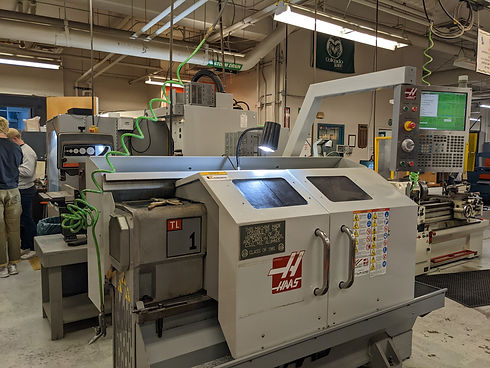

Screwdriver Manufacturing - Automation
Flathead
​
The most difficult part to automate would be the forging of the tool rod blank into the flathead. This would cost the most upfront. Forging both sides of the rod can be automated. One side would use a flathead dye and the other a swaged dye. Swaging the end is to ensure a good bond when casting.
​
Automating the heat treatment of the rod would be easy with a few robots. It would make sense to heat treat the rod before casting it into the aluminum.
​
Next, the casting of the aluminum around the tool rod can be automated. A mold can even be created to cast multiple screwdriver handles at once. Robots could place the rods into position and pour the molten aluminum into the blank.
​
Lastly, a CNC lathe can be used to turn and knurl the handle into the desired shape. This can be automated with a robot loading and unloading the machine.
​
Phillips
​
Injection molding is already one of the most automated manufacturing processes in the world. As the molds are easy to machine and inexpensive, setting up automation for this specific product would be relatively easy. This would allow for mass production and the price per screwdriver to dramatically decrease.